As a service provider in the self-adhesive industry with more than 30 years of experience, I personally think that the following three points are the most important:
1. Supplier qualifications: evaluate whether the supplier has a legal business license and relevant industry qualification certification.
2. Product quality: ensure that the self-adhesive materials provided by the supplier are of high quality and meet industry standards, such as CY/T 93-2013 "Printing Technology Self-adhesive Label Quality Requirements and Inspection Methods".
3. Production capacity: understand the production scale and capacity of the supplier to ensure that it can meet your order needs.
In addition, in detail, there are the following personal opinions, for reference only:
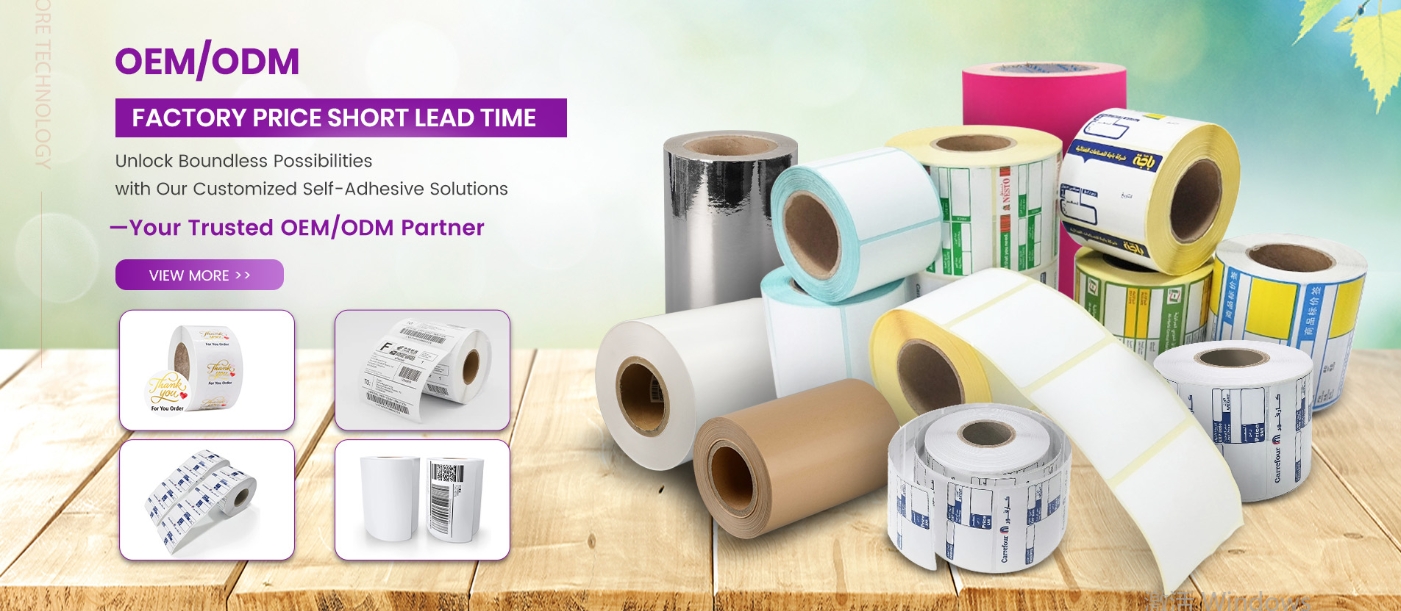
1. Determine your needs
Before choosing a self-adhesive supplier, you first need to clarify your specific needs. Here are a few key considerations:
1.1 Product type and label size
- Determine the type of self-adhesive material required, such as PE, PP or PVC, based on product characteristics and packaging requirements.
- Clarify the size specifications of the label, including length, width and shape, to ensure that the label matches the product packaging.
1.2 Quality requirements
- Determine the quality standards of the label, including viscosity, water resistance, temperature resistance, etc., to meet the needs of product use in different environments.
1.3 Application environment
- Consider the environmental conditions where the product is used, such as outdoor, high temperature, humid or ultraviolet environments, and select the corresponding adaptable self-adhesive materials.
1.4 Cost budget
- According to the budget, evaluate the cost-effectiveness of different materials and select cost-effective self-adhesive materials, while considering long-term costs and durability.
1.5 Environmental protection and sustainability
- Understand the environmental performance of self-adhesive materials and choose materials that meet environmental standards to reduce the impact on the environment.
1.6 Label design and printing requirements
- Select appropriate materials according to label design to ensure printing effect and quality, while considering the compatibility of printing equipment and technology.
1.7 Purchase quantity and inventory management
- Reasonably predict the purchase quantity based on actual demand, avoid inventory backlog or shortage, and establish an effective inventory management system.
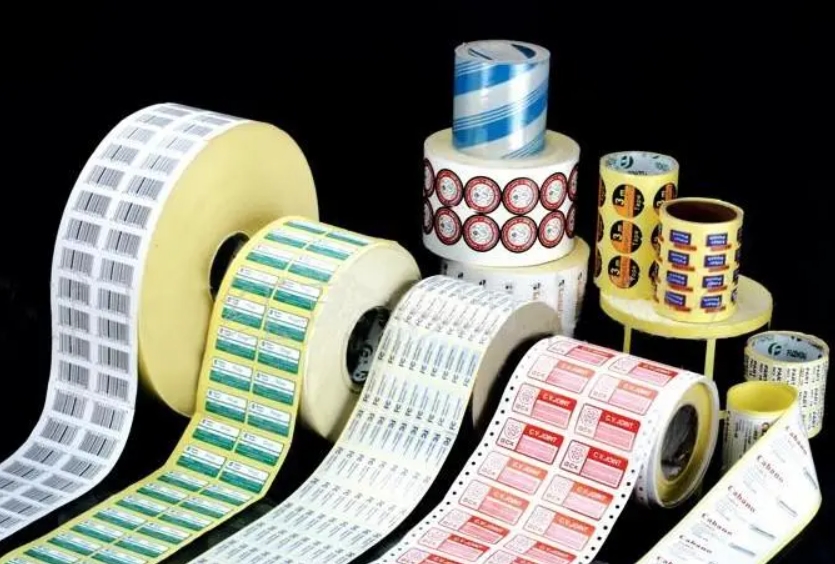
2. Evaluate supplier qualifications
2.1 Enterprise qualifications
Evaluating supplier qualifications is the first step in selecting a self-adhesive supplier. Enterprise qualifications include but are not limited to business licenses, industry certifications, quality management system certifications, etc. A qualified supplier should have a legal business license and relevant industry certifications, such as ISO 9001 quality management system certification, which indicates that its product quality management system meets international standards.
2.2 Production capacity
Production capacity is a key indicator to measure whether a supplier can meet order requirements. Investigate the supplier's production equipment, production line scale, technical maturity, and employee professional skills. For example, a supplier with modern production equipment and automated production lines can ensure high efficiency and high quality production of products.
2.3 Technical level and product R&D capabilities
Technical level and product R&D capabilities directly affect the performance and innovation of self-adhesive materials. Whether the supplier has an independent R&D team and whether it continues to invest in R&D to improve product performance and develop new products is an important aspect of evaluating its technical strength. For example, some suppliers may have multiple technical patents, which not only reflects its R&D strength, but also ensures the technological leadership of the product.
2.4 Quality assurance capabilities
Quality is the lifeline of an enterprise, and the quality of self-adhesive materials directly affects the performance and market competitiveness of the final product. The supplier's quality assurance capabilities include raw material inspection, production process control, finished product testing and other links. Whether the supplier has a complete quality management system and strict quality control process is an important basis for evaluating its quality assurance capabilities.
2.5 Business performance and financial status
Business performance and financial status reflect the market competitiveness and financial stability of the supplier. A supplier with stable performance and healthy finances is more likely to provide continuous and reliable supply services. You can learn about the supplier's operating conditions and profitability by consulting its annual report, financial statements and other public information.
2.6 Fulfillment of social responsibilities
Modern enterprises are paying more and more attention to social responsibilities. A supplier who actively fulfills social responsibilities is more trustworthy. Investigating whether the supplier complies with environmental laws and regulations, participates in social welfare activities, and has good labor relations are important aspects of evaluating the supplier's social responsibility.
2.7 Customer evaluation and market reputation
Customer evaluation and market reputation are direct feedback for evaluating the supplier's service level and product quality. You can learn about the supplier's service quality, delivery punctuality, problem-solving ability, etc. through customer recommendations, industry evaluations, online reviews and other channels. A supplier with good customer evaluation and market reputation is more likely to provide satisfactory services and products.
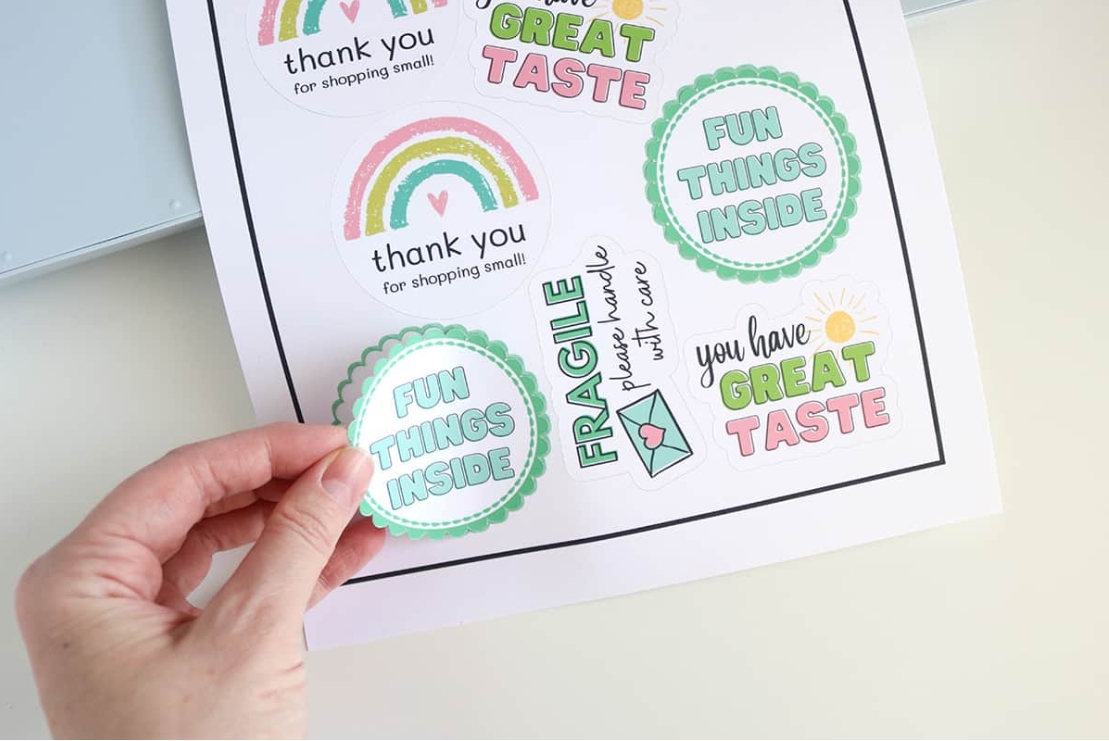
3. Product quality inspection
3.1 Appearance quality inspection
Appearance is the first impression of the product to consumers. For self-adhesive labels, the inspection of appearance quality is crucial. Inspection contents include:
- Surface flatness: Ensure that there are no defects such as bumps, wrinkles, bubbles, etc. on the label surface.
- Printing quality: Check whether the pattern is clear, the color is full, and there is no blur, fall-off or misalignment.
- Edge quality: The edges should be neat and straight, without burrs, misalignment or breakage.
3.2 Physical performance inspection
Physical performance is a key indicator for measuring the durability and reliability of self-adhesive labels. Inspection items include:
- Viscosity: The label should have appropriate viscosity, which can be firmly attached and easily removed, avoiding insufficient or excessive viscosity.
- Weather resistance: The label should maintain good adhesion under different environmental conditions, such as outdoor, high temperature and humid environment.
- Water resistance: Especially for labels used outdoors, they should have good water resistance and maintain stable adhesion in humid environments.
3.3 Packaging and labeling inspection
Packaging and labeling are important links in protecting product integrity and providing product information. Inspection points include:
- Packaging materials: Ensure that the packaging materials are suitable for protecting self-adhesive labels and preventing damage during transportation.
- Label information: Check whether the product label is clear and accurate, and contains necessary product information, such as production date, batch number, expiration date, etc.
3.4 Standard compliance and certification
Following relevant industry standards and obtaining certification is another important aspect to ensure product quality:
- Comply with standards: such as CY/T 93-2013 "Printing Technology Self-adhesive Label Quality Requirements and Inspection Methods" to ensure that the product meets industry standards.
- Certification acquisition: Passing ISO9001 and other quality management system certifications proves that the supplier has the ability to stably provide qualified products.
3.5 Inspection methods and tools
The use of correct inspection methods and tools is a prerequisite for ensuring the accuracy of inspection results:
- Visual inspection: Use standard light sources and appropriate tools to inspect the appearance of labels.
- Viscosity test: Use professional equipment to test the viscosity of labels to ensure that they meet standard requirements.
- Weather resistance and water resistance test: Simulate the actual use environment to test the weather resistance and water resistance of labels.
3.6 Quality Control Process
Establish a strict quality control process to ensure that each batch of products is strictly inspected:
- Sampling process: formulate sampling standards and processes to ensure that the samples are representative.
- Handling of unqualified products: mark, isolate and handle unqualified products to prevent them from entering the market.
- Continuous improvement: continuously optimize product quality and inspection processes based on inspection results and market feedback.
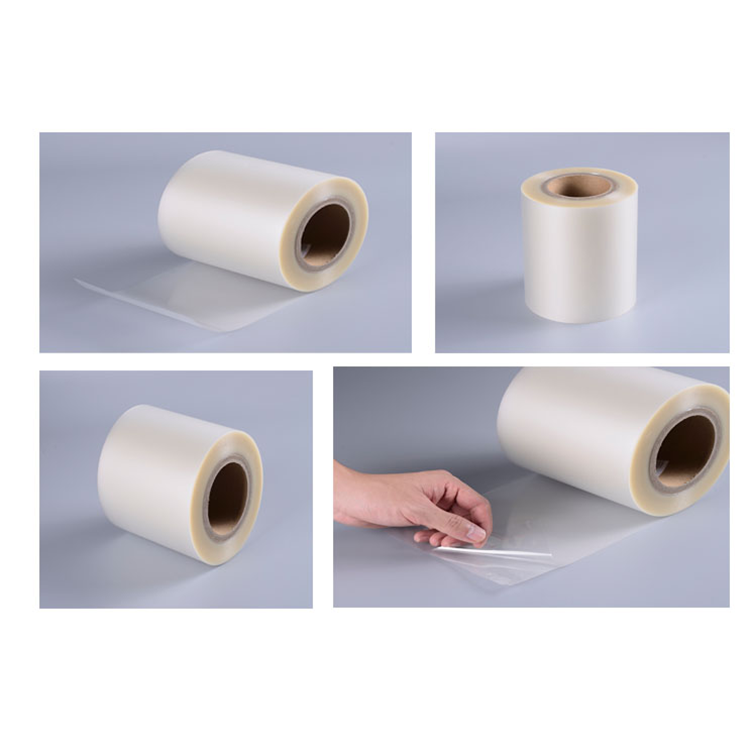
4. Price and cost analysis
4.1 Importance of cost accounting
For self-adhesive suppliers, cost accounting is a key link to ensure corporate profits and competitiveness. Through accurate cost accounting, suppliers can reasonably price and provide data support for potential cost control.
4.2 Cost structure analysis
The cost structure of self-adhesive mainly includes raw material cost, labor cost, manufacturing cost, etc. Specifically:
- Raw material cost: including the cost of basic materials such as paper, glue, ink, etc., which is the main part of the cost.
- Labor cost: covers the wages of workers directly involved in production and the salaries of managers.
- Manufacturing expenses: including fixed costs of factory operations such as equipment depreciation and power costs.
4.3 Price strategy
When formulating a price strategy, suppliers need to consider factors such as cost markup, market competition, and customer demand. Prices not only reflect costs, but also ensure reasonable profit margins and market competitiveness.
4.4 Cost control measures
Effective cost control can improve the market competitiveness of suppliers. Measures include:
- Optimize raw material procurement: reduce unit prices through bulk procurement and select cost-effective raw materials.
- Improve production efficiency: reduce waste and increase unit output through technology upgrades and process optimization.
- Reduce indirect costs: reasonably plan the management structure and reduce unnecessary management expenses.
4.5 The dynamic relationship between cost and price
There is a dynamic relationship between cost and price. Factors such as market price fluctuations and changes in raw material costs will affect the price of the final product. Suppliers need to flexibly adjust their cost control strategies to adapt to market changes.
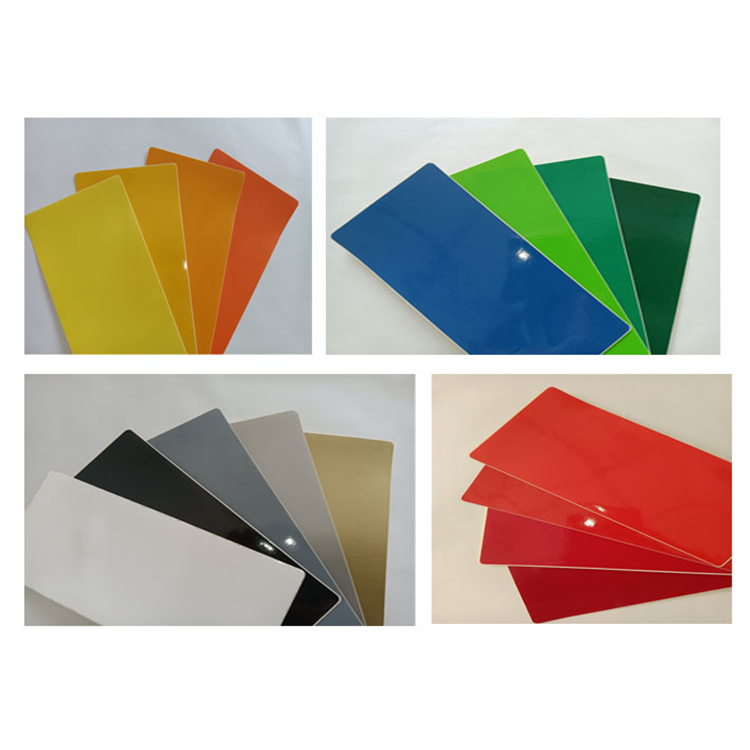
5. Service and support considerations
5.1 Technical support capabilities
When choosing a self-adhesive supplier, technical support is one of the important considerations. Whether the supplier has a professional technical team and can provide timely and effective technical support and solutions is crucial to ensure the smooth production process. According to market analysis, high-quality suppliers usually have the following characteristics:
- Technical team: Have a professional technical team whose members have rich industry experience and professional background.
- Response speed: Able to respond quickly to customer needs and problems and provide timely technical support.
- Solutions: Able to provide customized solutions based on the specific needs of customers.
5.2 Customer Service Level
Customer service is another key indicator to measure the quality of supplier services. Excellent customer service can improve customer satisfaction and establish long-term cooperative relationships. The following are several aspects to evaluate customer service levels:
- Service attitude: Whether the supplier has a positive service attitude and can patiently answer customer questions.
- Service channels: Whether to provide a variety of service channels, such as telephone, email, online customer service, etc., to meet the needs of different customers.
- Service efficiency: How efficient is the problem solving, whether it can solve customer problems within the promised time.
5.3 After-sales service system
A complete after-sales service system can provide customers with continuous support and reduce worries. The following are several key points for evaluating the after-sales service system:
- Warranty policy: Does the supplier provide a clear product warranty policy and is the warranty period reasonable?
- Repair service: Does it provide convenient repair services, and what is the repair response time and repair quality?
- Accessories supply: Can it provide sufficient accessories to reduce production delays caused by accessories problems?
5.4 Continuous improvement and innovation
Whether the supplier has the ability to continuously improve and innovate is also an important aspect of service and support considerations. This is not only related to whether the supplier can meet customer needs in the long term, but also to its competitiveness in the industry. When evaluating, you can consider:
- Improvement mechanism: Does the supplier have a complete product improvement and feedback mechanism, and can continuously optimize products based on market and customer feedback.
- Innovation ability: Does the supplier have the ability to develop new products to adapt to market changes and new customer needs.
- Technology update: Does the supplier regularly update technology to maintain the advancement and competitiveness of the product.
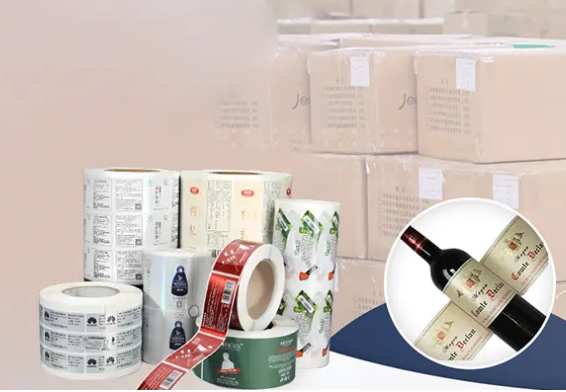
6. Geographic location and logistics
Geographic location is an important consideration for selecting a self-adhesive supplier, which directly affects logistics costs, delivery time and supply chain stability.
6.1 Impact of logistics costs
The geographical location of the supplier determines the transportation cost. Choosing a supplier with a close geographical location can significantly reduce logistics costs, especially when purchasing in bulk, and the savings in transportation costs can be converted into profits for the company.
6.2 Delivery time
The geographical location of the supplier also affects the delivery time. Suppliers with a closer geographical location can provide faster delivery, which is crucial for companies that need to respond quickly to market demand.
6.3 Supply chain stability
The suitability of the geographical location is also related to the stability of the supply chain. Under the influence of unpredictable factors such as natural disasters or political unrest, suppliers with a closer geographical location may be more able to ensure the continuity of the supply chain.
6.4 Response strategy
When choosing a self-adhesive supplier, companies should consider establishing a diversified supplier network, including geographically dispersed suppliers, to reduce the risks of a single supplier due to geographical location.
6.5 Technology and facilities
In addition to geographical location, the logistics facilities and technology of the supplier are also important considerations. An efficient logistics management system and advanced warehousing facilities can improve logistics efficiency and reduce the loss of goods during transportation.
6.6 Environmental factors
Environmental factors, such as climatic conditions, may also affect logistics efficiency. For example, extreme weather may delay the transportation of goods, so it is wise to choose suppliers that can adapt to the local environment and have countermeasures.
6.7 Comprehensive evaluation
When selecting a self-adhesive supplier, companies should comprehensively evaluate the various potential impacts of the geographical location, including cost, time, stability and environmental factors, to make the best decision.
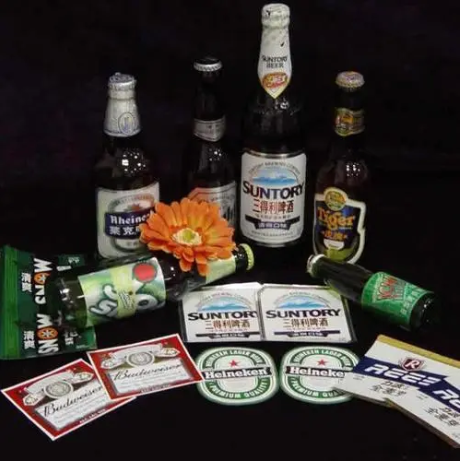
7. Environmental protection and sustainability
7.1 Environmental standards and certifications
When selecting a self-adhesive supplier, environmental standards and certifications are key considerations. Whether the supplier has ISO 14001 environmental management system certification and whether it complies with more specific environmental regulations such as the EU's RoHS directive are important criteria for evaluating its environmental commitment. In addition, whether the supplier uses recyclable materials or bio-based materials is also an important indicator of its environmental performance.
7.2 Sustainability practices
The supplier's sustainability practices include its energy use, waste management and protection of water resources during the production process. A good self-adhesive supplier will adopt energy-saving technologies to reduce carbon footprint, implement waste reduction and recycling programs, and take measures to protect water resources to ensure that its production activities do not have a negative impact on the environment.
7.3 Green Supply Chain Management
Green supply chain management is the key to ensuring that the entire production and supply chain process meets environmental protection and sustainability requirements. Whether the supplier has implemented a green procurement policy, selected environmentally friendly materials, and cooperated with suppliers who also focus on sustainable development are important aspects of evaluating its sustainability performance.
7.4 Environmental Impact Assessment
Suppliers should conduct environmental impact assessments regularly to identify and reduce the potential impact of their production activities on the environment. This includes evaluating the impact of various links such as raw material procurement, production process, product use and disposal on the environment, and taking measures to improve them.
7.5 Social Responsibility
In addition to environmental factors, the social responsibility of suppliers is also an important part of sustainability. This includes ensuring that their employees enjoy fair working conditions, reasonable wages and a safe and healthy working environment, as well as assuming social responsibilities in the community, such as supporting local education and charity activities.
7.6 Customer and Market Demand
As consumers’ demands for environmentally friendly and sustainable products grow, suppliers need to keep up with market trends and provide self-adhesive products that meet these demands. This may mean developing new environmentally friendly materials, or improving existing products to reduce their impact on the environment.
7.7 Regulatory Compliance and Transparency
Suppliers should comply with all relevant environmental regulations and maintain transparency in supply chain management. This means disclosing their environmental policies, practices and achievements, as well as reporting environmental issues when they occur.
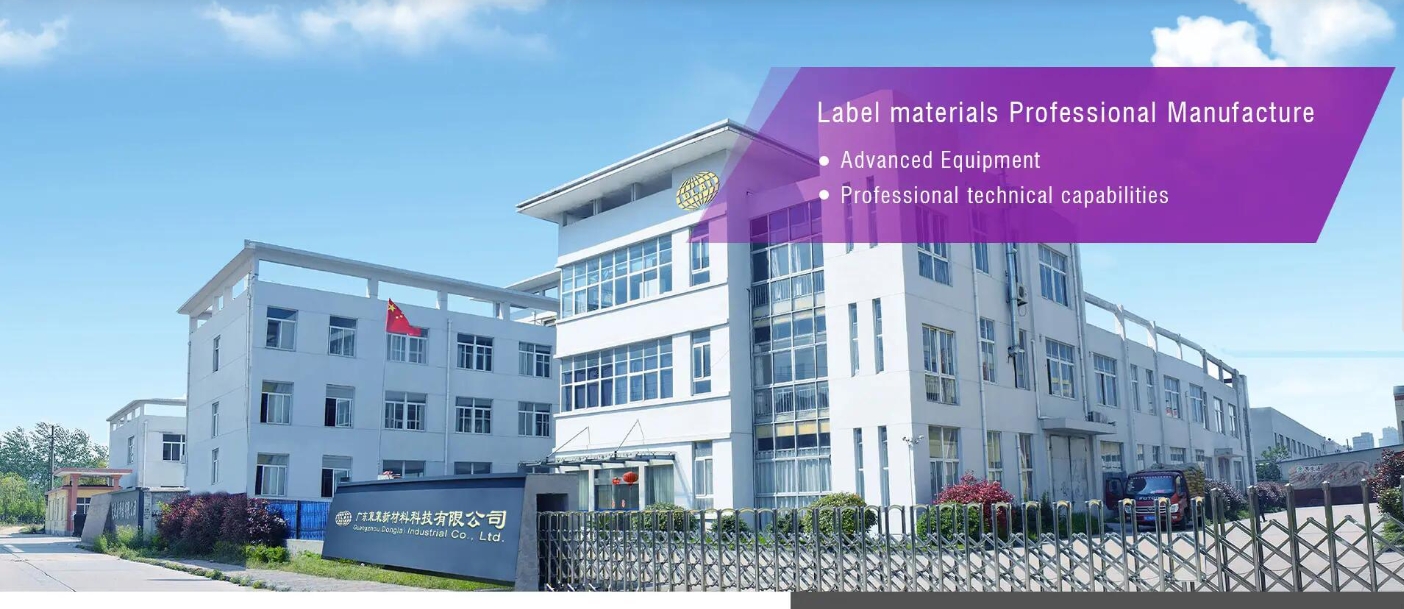
Contact us now!
Over the past three decades, Donglai has achieved remarkable progress and emerged as a leader in the industry. The company's extensive product portfolio comprises four series of self-adhesive label materials and daily adhesive products, encompassing more than 200 diverse varieties.
With an annual production and sales volume exceeding 80,000 tons, the company has consistently demonstrated its capability to meet the market demands on a large scale.
Feel free to contact us anytime! We're here to help and would love to hear from you.
Adress: 101, No.6, Limin Street, Dalong Village, Shiji Town, Panyu District, Guangzhou
Phone: +8613600322525
mail: cherry2525@vip.163.com
Sales Executive
Post time: Aug-13-2024